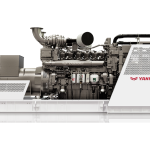
Modelo 01
June 24, 2024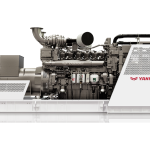
BENDING ROBOT.
Programmed in synchronisation with
the numerical control of the panel
bender machine.
BENDING MACHINE
ROBOT WELDING
2,000 KG LOAD CAPABILITY
5,000 mm LENGTH CAPABILITY
GK2 1mm WELDING WIRE
120-200A INTENSITY
+16% CO2 ARGON GAS
MANUAL WELDING
2 WELDING CELLS
2 REWORKING CELLS
LINE CAPABILITY
CNC CONTROLLED
ROCKWOOL & FOAM
VOLCANIC ROCKWOOL AND ISOVER
DENSITY 145KG/M3
CLASS M0
WORKING Tº UP TO 750ºC
WATER JET
PRE-ASSEMBLY CELLS OF PARTS FOR FINAL ASSEMBLY
The insulating material as well as small pieces are assembled onto the already painted piece to make an assembled unit, which will be subsequently mounted on the assembly line.
OPERATIONS
50,000 CONTROL PANELS PER YEAR
(POWER AND CONTROL PANELS, DISTRIBUTION PANELS, EXTERNAL PANELS)
WIRING INSTALLATIONS
IN HOUSE DESIGN AND ASSEMBLING
HIMOINSA MADE CONTROLLERS
HARDWARE AND SOFTWARE
(EPLAN, PRO PANEL, INVENTOR, AUTOCAD)